Le cycle de l’aluminium
Le cycle de l’alu
La bauxite est le minerai de base qui sert à la fabrication de l’aluminium. Son nom découle des baux de Provence où elle a été découverte au dix-neuvième siècle. En utilisant le procédé Bayer, on extrait l’alumine (AL2O3) du minerai qui va servir à la fabrication de l’aluminium dit primaire. Cette Alumine est ensuite réduite par une réaction d’électrolyse et en utilisant une anode en carbone. Afin de réduire l’empreinte carbone de l’aluminium primaire, les société Rio Tinto et Alcoa ont créé une entreprise Elysis qui travaille sur la substitution de l’anode carbone par une anode céramique qui réduira l’empreinte carbone de 1,5 tonne/tonne d’aluminium.
L’Aluminium est un matériau permanent qui peut être recyclé à l’infini. Son recyclage permet de réduire la consommation d’énergie de plus de 90%. Il est donc primordial de le recycler car ‘l’investissement’ de départ en énergie électrique peut être très largement compensé par les différents cycles de recyclage. On comprend bien que la collecte de toute chute de fabrication et de tout morceau d’aluminium en fin de vie est importante afin que l’économie circulaire de ce matériau soit réalisée.
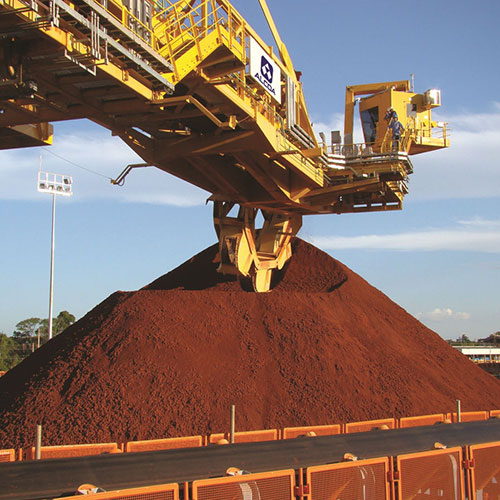
L’aluminium de première fusion
L’aluminium de première fusion est fabriqué selon deux grandes étapes :
L’extraction de l’alumine :
On extrait dans un premier temps la bauxite qui est composée au maximum de 75 % d’alumine hydratée. Celle-ci est pulvérisée puis mélangée à de la soude caustique à haute température et sous pression. Ceci à pour effet de dissoudre l’alumine et de créer de l’aluminate de sodium. Les 25 % qui restent sous forme solide sont simplement filtrés.
Ensuite on ajoute du tri-hydrate d’alumine pur très fin ce qui permet de former des cristaux qui sont séparés de la soude caustique par filtration.
Les cristaux sont calcinés à environ 1000 °C. La chaleur fait évaporer l’eau et il reste alors de l’oxyde d’aluminium ou de l’alumine calcinée.
Il faut quatre tonnes de bauxite pour obtenir deux tonnes d’alumine qui donne une tonne d’aluminium.
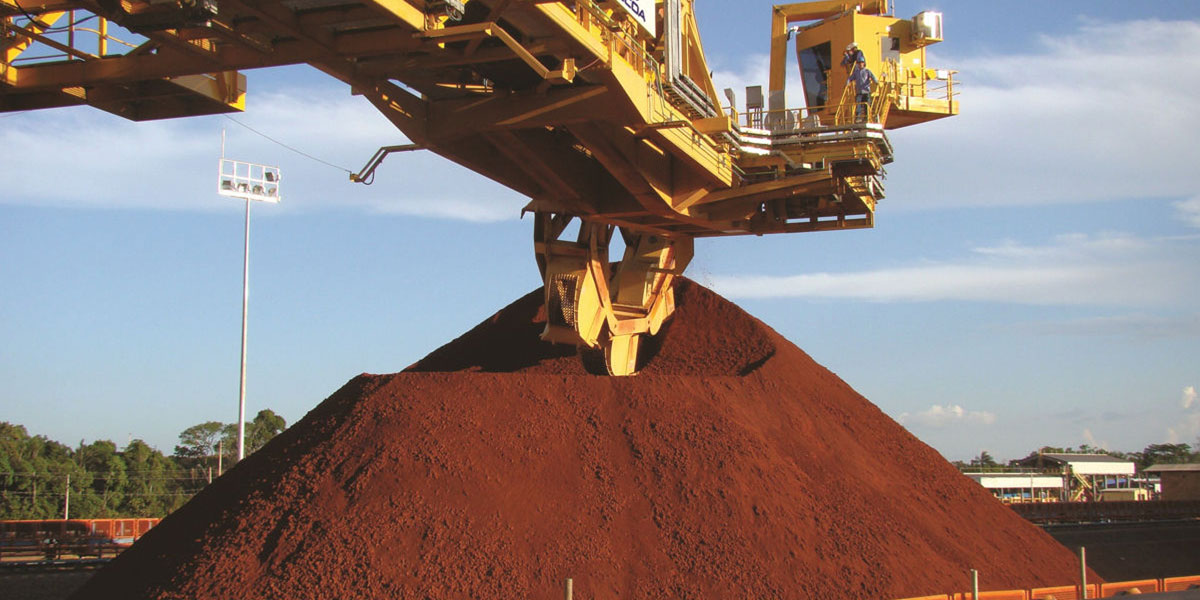
La production de l’aluminium :
L’aluminium est fabriqué à partir de l’alumine grâce au procédé électrolytique « Hall-Héroult ».
Cela se déroule dans de grandes cuves traversées par un courant continu de haute intensité (500 000 Ampères).
Les cuves, qui forment la cathode, sont fabriquées à partir de carbone graphite. Les anodes, elles aussi sont en carbone graphite, sont complémentement consommée durant le procédé en environ 20 jours.
Ce procédé va réduire l’alumine et former de l’aluminium. C’est un procédé énergivore qui nécessite environ 13 kWh par kilogramme d’aluminium.
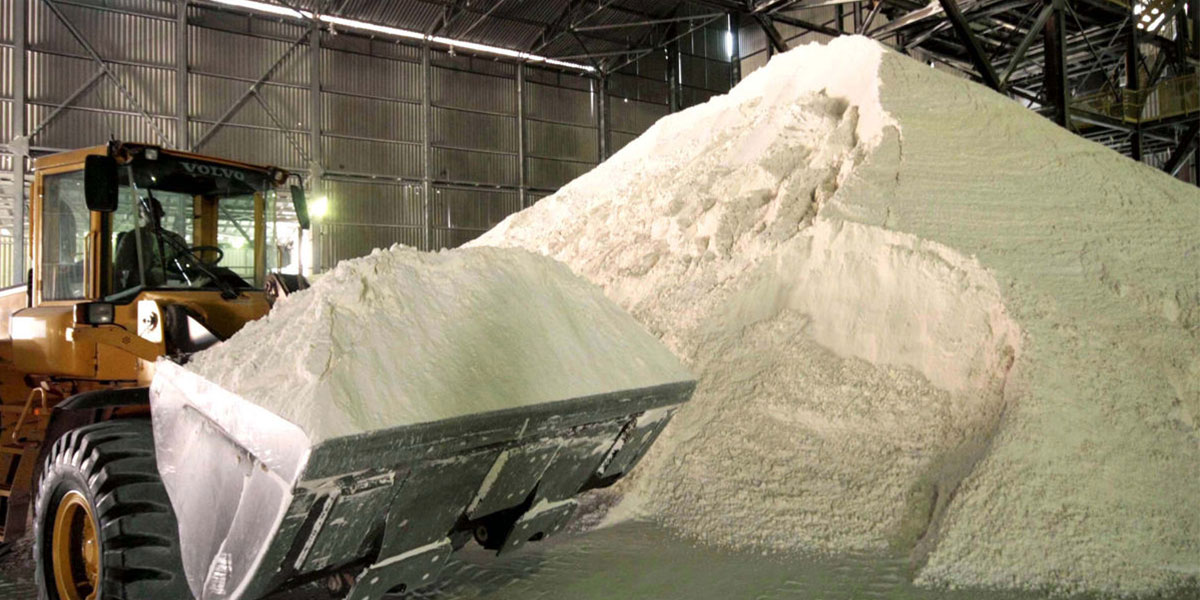
L’aluminium ainsi produit est dirigé vers une fonderie pour être allié à d’autres métaux. Puis il sera transformé par différents procédés comme le laminage et l’extrusion.
Une fois entré dans le cycle de recyclage ce métal nécessitera 95 % d’énergie en moins.
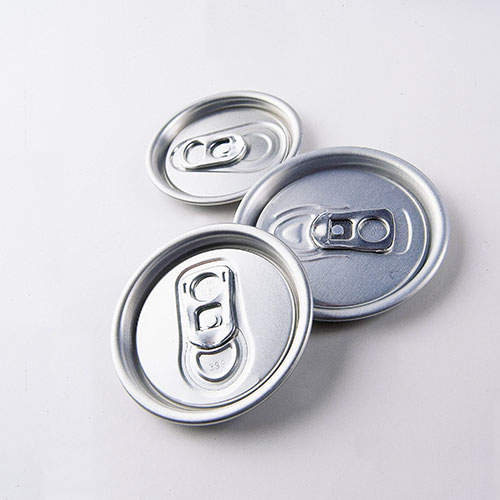
Seconde fusion: Le recyclage à l’infini
La seconde fusion concerne les produits recyclés.
Les économies:
Il faut savoir que tous les produits à base d’aluminium peuvent être recyclés à l’infini c’est pourquoi ils ne doivent pas être considérés comme des déchets mais comme des matières premières.
Grâce à l’aluminium recyclé on économise pour 1 kg d’aluminium 13 kWh, 4 kg de bauxite et 4 kg de produits chimiques
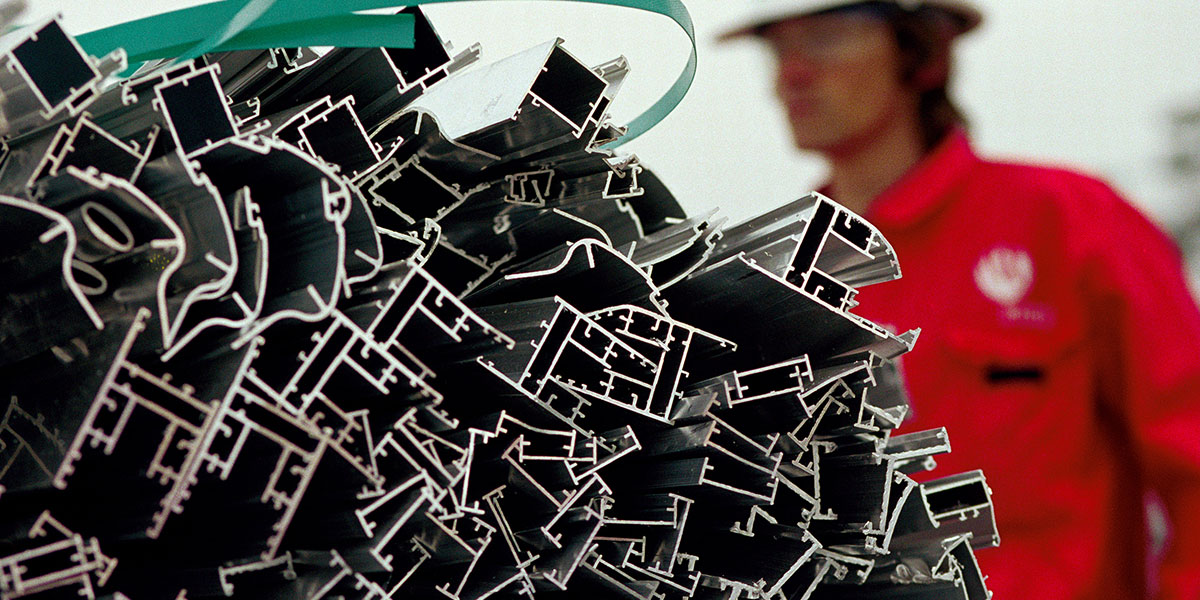
Les applications de l’aluminium recyclé :
L’aluminium recyclé se retrouve dans toutes les applications de l’aluminium de première fusion (Il ne perd aucune de ses propriétés physiques) : nouveaux emballages, moteurs de voitures, capots de tondeuses à gazon, semelles de fers à repasser, radiateurs, mobilier contemporain….et, en général, la majorité des objets en aluminium moulé.
Dans le secteur de l’automobile, on recycle également une grande part de la production. 100 % des pièces de voiture en aluminium sont recyclables, et la quantité d’aluminium utilisée dans les voitures augmente chaque année.
L’aluminium se recycle indéfiniment
Aujourd’hui, près de 30 % de l’aluminium utilisé provient du recyclage
Le recyclage de l’aluminium permet une économie d’énergie qui peut atteindre 95 % par rapport à la production du métal de première fusion.
La vie de l’aluminium est donc infinie, très écologique et très économique alors ne le gâchons pas. Contribuons à son recyclage.
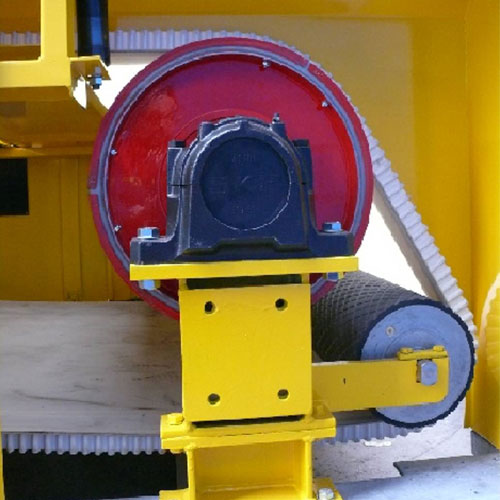
La machine à courant de Foucault (MCF)
Fonction :
Les ordures ménagères incinérées contiennent des emballages et des objets en aluminium. Lors de la collecte sélective les emballages fabriqués à partir de différents matériaux (carton, papier, plastique, acier,…) sont mélangés pour être envoyés aux centres de tri.
L’extraction de l’aluminium est alors effectuée par machine à courant de Foucault. En ce qui concerne les centres de tri en France, plus de 40 centres de tri sont équipés de 2 machines à courant de Foucault. Ce nombre de CDT couvre plus d’un tiers de la population française.
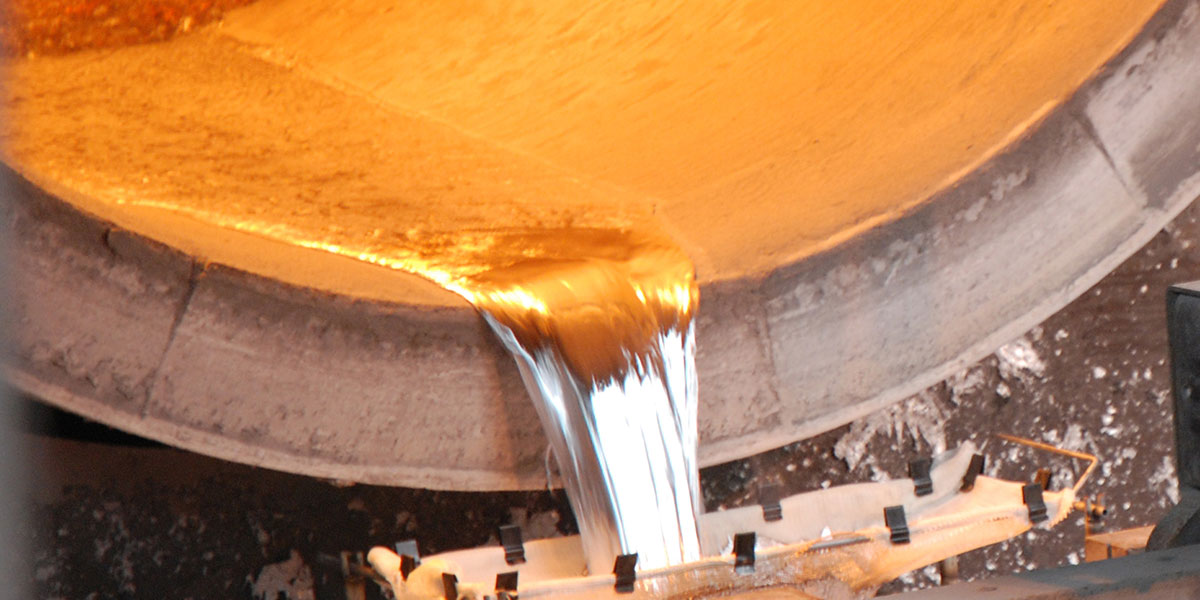
Fonctionnement : Pour les centres de tri
La machine à courant de Foucault permet de récupérer automatiquement l’aluminium. Il s’agit d’une roue polarisée qui tourne à 2600tr/mn, en fin du tapis sur lequel circulent les déchets. La roue polaire composée en périphérie de pôles d’aimant nord et sud alternés, crée par sa rotation un champ magnétique alternatif. Ce champ magnétique alternatif induit un courant alternatif dans les emballages aluminium passant à proximité. L’opposition de phase entre le champ magnétique alternatif de la roue polaire et le champ magnétique résultant du courant alternatif induit dans l’aluminium, provoque l’éjection des emballages aluminium
Selon leur poids, les emballages aluminium ne vont pas réagir de la même manière :
– Les produits légers comme les feuilles d’aluminium froissées sont éjectés à l’horizontale
– Les autres, comme les boîtes boisson, sont éjectés selon une trajectoire parabolique.
Ainsi il sont séparés dans deux bacs distincts et pourront être recyclés de manière différente.
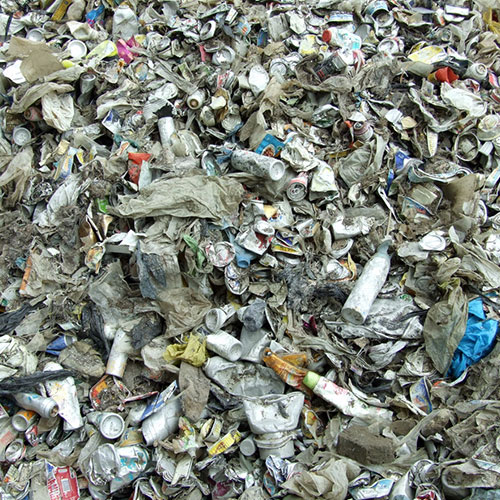
Le tri mécano biologique (TMB)
Le tri mécano biologique s’applique aux ordures ménagères résiduelles. C’est- à- dire à toutes les ordures qui n’ont pas été triées par la population et qui finissent dans la poubelle noire.
Il permet de réduire la quantité de déchets enfouis en récupérant le maximum de déchets valorisables de ces ordures.
La France compte une quarantaine de projets de création de sites de TMB, ainsi qu’une vingtaine de projets de transformation de sites existants de compostage d’ordures ménagères. Le tout concerne près de 3 millions de tonnes de déchets par an.
Le tri mécano biologique compte plusieurs étapes de traitement des déchets :
– Les déchets arrivent au centre de traitement. Un premier tri est effectué afin de retirer les déchets de très grande taille comme les palettes.
– Le reste des déchets passe dans un trommel (long tube rotatif parsemé de trous de différentes tailles afin de séparer les déchets par taille). Le trommel sépare les déchets par fractions :
– inférieurs à 80 mm
– entre 80 et 200 mm
– et supérieurs à 200mm
Ensuite chaque type de déchet est traité différemment.
Les déchets supérieurs à 200 mm sont composés principalement de cartons et de ferraille. Ils passent dans une cabine de tri où les cartons sont séparés manuellement du reste
– les cartons sont stockés puis envoyés aux usines de recyclage. La ferraille est séparée des autres déchets et envoyée aux usines sidérurgiques.
– Le reste des déchets sera soit stocké pour enfouissement soit utilisé dans une unité de valorisation énergétique.
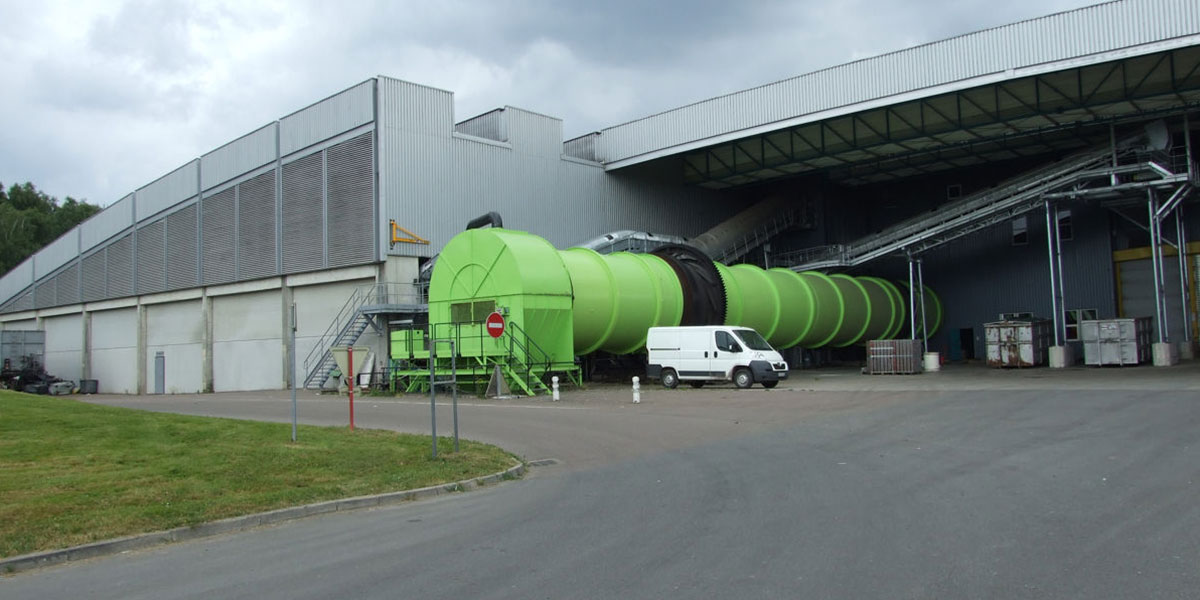
Les déchets entre 80 et 200 mm :
– Ces déchets sont tout d’abord déferraillés (les métaux ferreux sont extraits des autres déchets). Les métaux ferreux seront stockés pour être envoyés dans leur usine de recyclage.
– Les autres déchets vont passer dans une machine à courant de Foucault (vous trouverez ici l’explication concernant cette machine). Cette machine sépare les métaux non-ferreux du reste des déchets.
– Les métaux non-ferreux (dont l’aluminium) sont stockés pour être envoyés dans leur centre de recyclage. France Aluminium Recyclage peut vous aider dans cette étape à trouver l’acheteur qui reprendra l’aluminium que vous avez trié.
– Le reste des déchets est trié entre corps plats et corps creux.
– Les corps creux passent dans un système de tri optique qui permet de séparer les PET, les PEHD et les HautPCI.
> PET : polyéthylène téréphtalate : principalement les bouteilles boisson
> PEHD : polyéthylène haute densité : emballages de produits détergents, bouteilles de lait, bouteilles de shampoing, flacons de médicaments, bouchons de bouteilles boissons, tubes pour le transport du gaz ou de l’eau
> Haut PCI : Haut pouvoir calorifique inférieur : papiers cartons et plastiques
Puis les autres déchets qui passent en unité de valorisation énergétique ou en enfouissement.
– Les corps plats sont stockés en tant que Haut PCI.
Les déchets inférieurs à 80mm :
– Ils passent dans un système de déferraillage qui sépare les ferrailles des autres déchets.
– Les autres déchets passent dans un séparateur balistique qui permet de séparer les matières organiques des autres déchets (qui sont enfouis ou en valorisés énergétiquement).
– Les matières organiques restantes servent de composte.
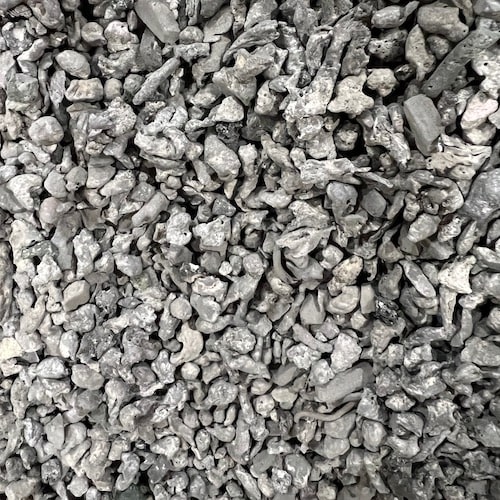
Les mâchefers d’incinération
Les ordures ménagères entrant dans un incinérateur contiennent encore des emballages en aluminium qui n’ont malheureusement pas été captés/triés en amont.
A la sortie de l’incinérateur, les matériaux non combustibles sont récupérés sous forme de mâchefers. Ils contiennent des matières minérales inertes, en moyenne 10% de métaux ferreux et 1% de nodules de métaux non-ferreux composés majoritairement d’aluminium partiellement ou totalement fondu dans l’incinérateur, puis solidifiés dans les mâchefers.
Leur extraction s’effectue par machine à courant de Foucault (vous trouverez l’explication dans la section « machine à courant de Foucault »)
Actuellement 50 % des mâchefers issus de l’incinération sont ainsi récupérés. Le potentiel restant est donc très important
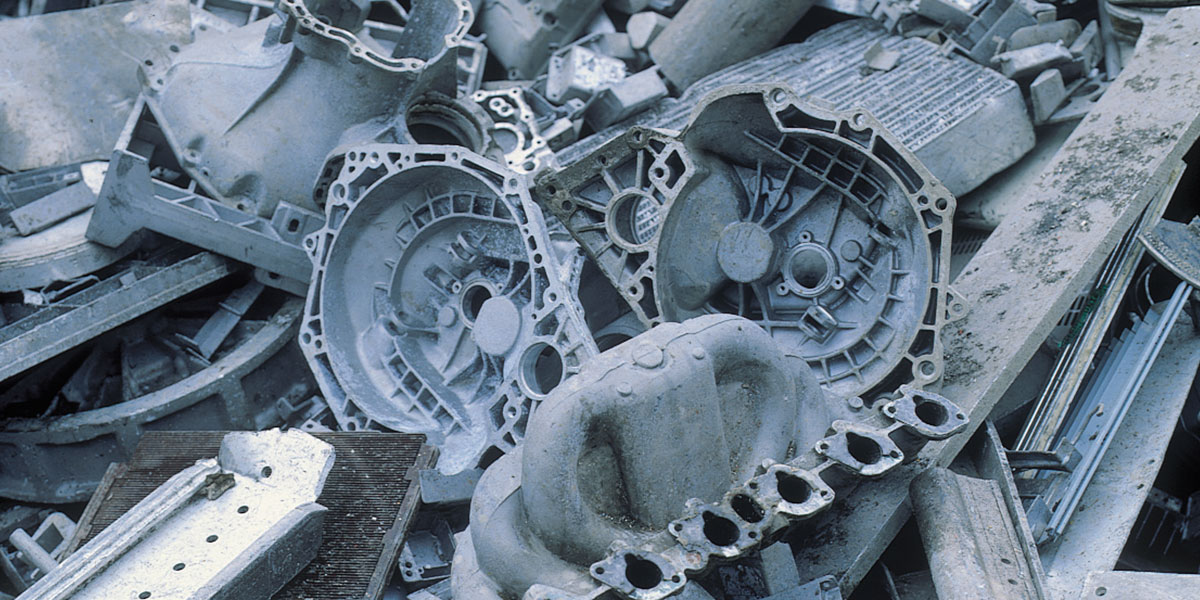
Rentabilité :
Nous vous aidons dans notre onglet «Collectivité on vous aide » à calculer la rentabilité d’une installation de MCF.
Nous allons vous donner ici quelques conseils sur le choix de cette installation.
Premièrement afin que cette machine soit rentable il faut réaliser des économies d’échelle
Nos conseils :
– Minimum de 100 tonnes de nodules d’aluminium (les petites collectivités regroupent le traitement des mâchefers de plusieurs petits incinérateurs sur une plate-forme unique)
– L’économie d’échelle n’est plus très importante à partir de 200 tonnes (soit 20 000 tonnes de mâchefers, ce qui correspond au tonnage issu d’une ville de 200 000 habitants).
Le coût d’une machine à courant de Foucault installée est de l’ordre de 50 000 à 150 000 € selon sa taille, ses caractéristiques et les équipements périphériques nécessaires.
Notre conseil : l’intégration de cet équipement dès la conception de l’ensemble du site permet de réduire notablement les coûts.
Les coûts de fonctionnement annuels (électricité, entretien et maintenance) se situent entre 4 et 8 % de la valeur de l’investissement.
Soit pour un investissement de 100 000 € entre 4000 et 8000€
L’exploitation d’une machine à courant de Foucault apporte deux types de recettes :
– La vente : le prix moyen de reprise des nodules de métaux non-ferreux est de 600 €/tonne. Ce prix est fonction de la qualité des nodules d’aluminium et du cours de l’aluminium à la Bourse des métaux de Londres (LME).
– Le soutien Eco-Emballages : 76 € à la tonne extraite.
Il ne faut pas négliger l’économie réalisée sur l’enfouissement des déchets qui est de l’ordre de 80 à 100€ la tonne.
En résumé pour une collectivité de 200 000 habitants, et une teneur moyenne en nodules de métaux non-ferreux de 1%, un tel équipement est amorti en 4 à 5 ans.
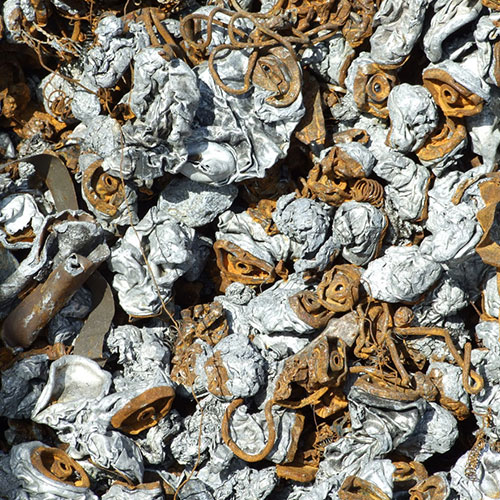
La pyrolyse
Fonction :
La pyrolyse permet de recycler tous les emballages légers en aluminium qui jusqu’ici étaient brûlés dans les incinérateurs.
En raison de leur taille et de leur épaisseur, le recyclage des emballages légers en aluminium par procédé conventionnel n’est pas optimal. Il est donc important d’utiliser la pyrolyse pour les recycler.
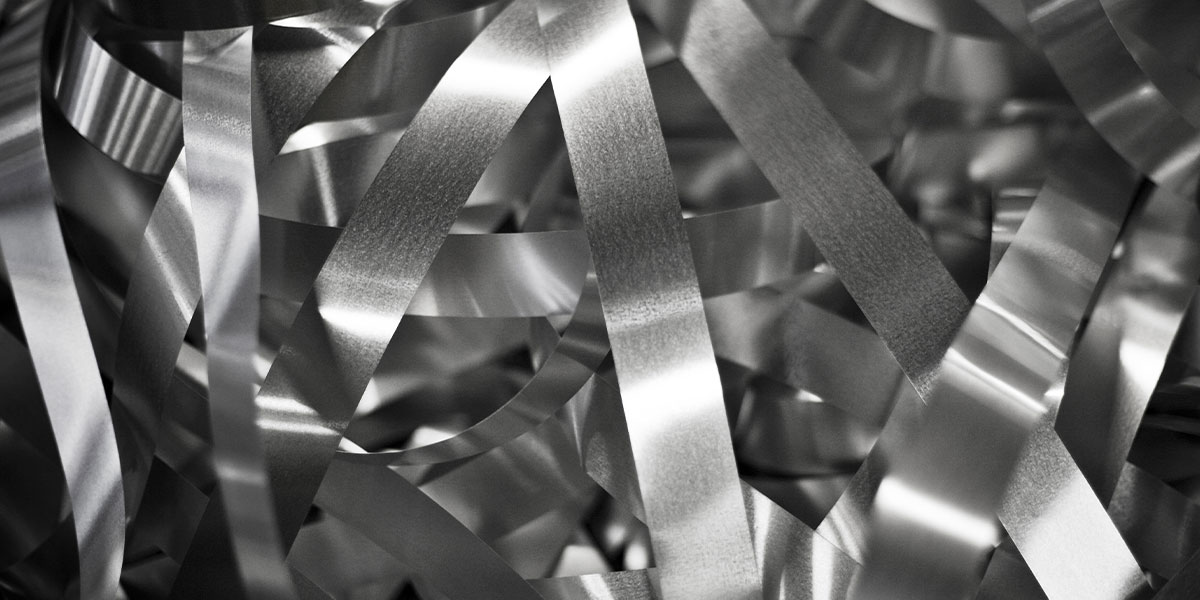
Fonctionnement :
Cette technique consiste à porter les emballages à une température comprise entre 500 et 550°C dans une atmosphère pauvre en oxygène afin d’éviter la fusion de l’aluminium
Les produits organiques (vernis, laques ou plastiques) sont ainsi décomposés en produits légers. Ils sont ensuite brûlés alors que l’aluminium reste intact (ce qui ne serait pas le cas dans le circuit classique)
La pyrolyse permet d’obtenir des granulats, des poudres ou des fragments d’emballages.